Seamless Pipe Manufacturing Process – Summary
Presently seamless pipe is made from round billet, which is pierced through the center to make it a hollow shell and then rolled or extruded and drawn to size. The seamless pipe manufacturing process consists of the following principal stages:
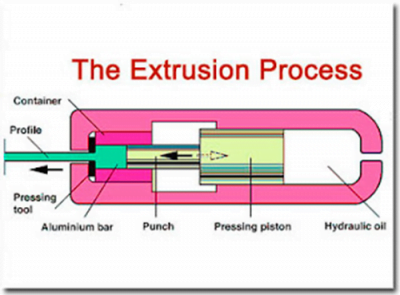
Extrusion Process [Image Source: From Web]
- Making of a hollow pipe shell in the piercing or extrusion operation
- Elongating the hollow pipe shell by reducing its diameter and wall thickness
- Making of a final pipe in the hot or cold rolling process
We hope the following information is helpful and you will learn more about how some tube manufacturing occurs.
Mandrel Mill Process

Mandrew Mill Process [Image Source: From Web]
- This process is used to make smaller sizes of seamless pipe, typically 1 to 6 inches (25 to 150 mm) diameter.
- The ingot of steel is heated to 2,370 °F (1,300 °C) and pierced.
- A mandrel is inserted into the tube and the assembly is passed through a rolling (mandrel) mill.
- Unlike the plug mill, the mandrel mill reduces wall thickness continuously with a series of pairs of curved rollers set at 90° angles to each other.
- After reheating, the pipe is passed through a multi -stand stretch-reducing mill to reduce the diameter to the finished diameter.
- The pipe is then cut to length before heat treatment, final straightening, inspection, and hydrostatic testing.
Mannesmann Plug Mill Pipe Manufacturing Process
Mannesmann Plugmill Process [Image Source: From Web]
- This process is used to make larger sizes of seamless pipe, typically 6 to 16 inches (150 to 400 mm) diameter.
- An ingot of steel weighing up to two tons is heated to 2,370 °F (1,300 °C) and pierced.
- The hole in the hollow shell is enlarged on a rotary elongator, resulting in a short thick-walled tube known as a bloom.
- An internal plug approximately the same diameter as the finished diameter of the pipe is then forced through the bloom.
- The bloom containing the plug is then passed between the rolls of the plug mill.
- Rotation of the rolls reduces the wall thickness
- The tube is rotated through 90° for each pass through the plug mill to ensure roundness.
- The tube is then passed through a reeling mill and reducing mill to even out the wall thickness and produce the finished dimensions.
- The tube is then cut to length before heat treatment, final straightening, inspection, and hydrostatic testing.
Pilgering & Cold Drawing Process for Producing Smaller Size Seamless Tubes from Larger Size Pipes
Pilgering and Cold Drawing Process [Image Source: From Web]
In general, the pilgering process has two primary purposes:
- One, and most importantly, pilgering is a cold working process that greatly improves the material grain structure.
- Two, it is a way of reducing large amounts of the outside diameter and inside diameter of a preexisting tube very quickly. Reduction rates can be as high as nearly 90% on some alloys. The cold mill pilgering process uses ring dies and a tapered mandrel to reduce tube cross sections by up to 90 percent.
The cold drawing process performs similar work to pilger process but the size reduction rates are restricted to generally 15 to 35% depending on the type of alloy.
Source: Various Websites from the Web, Wikipedia
Established in 1975, the Metallica Metals Group has its operations spread across major cities in India. We are a pioneer in the stainless steel pipes, carbon steel pipes and alloy steel pipes manufacturing and processing industry. Our products are exported to over 70 countries across the world, while in India we have supplies to even the remote areas. With over 250 tons of sale in stainless steel, alloy steel and carbon steel pipes every day, Metallica has emerged as a prominent vendor for many buyers in India and Overseas.
Our annual sales volume over 70,000 tonnes in India and Worldwide, has won us the dealership and distributorship of renowned seamless (JINDAL, ISMT) and welded steel pipes manufacturing companies across the globe.
Leave A Comment