Material selection is one of the most crucial decisions made in the design, manufacture, and application of large structural components. Material selection naturally influences the entire performance of the design, and thus it is critical that informed decisions are made during the design stage. Steel castings and steel forgings are two alternatives for large structural components. Each process has its advantages and disadvantages. This blog will present an honest evaluation of castings and forgings, so that those in the design community can make an informed choice.
Casting:-
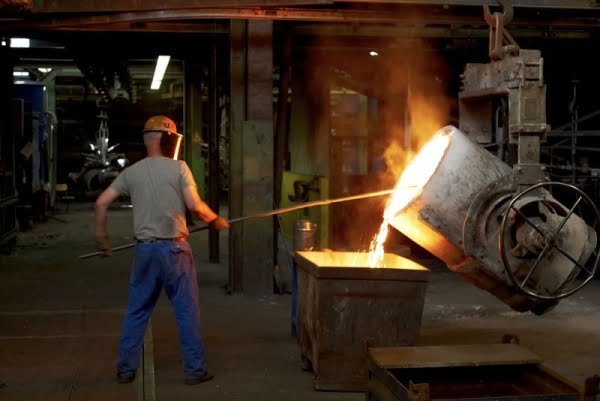
Steel Casting Method
Cast products are made by completely melting the material into a liquid state and then pouring it into a mold to solidify. The material takes the mold’s shape as it cools and is then removed from the mold once solidified. A cooking pan is one example of an everyday item made by casting with iron.
Applications of Casting: –
We use castings for a wide range of wear parts and components that are too large, complicated, intricate or otherwise unsuitable for the forging process. We can forge parts up to 50kgs but the sheer energy required to forge larger items make casting a much more viable alternative.
Casting Methods: –
- Investment Casting: – Investment Casting is the term applied to precision molding using a metal die and ceramic coating in which the chosen metal is injected. The mold material generally used is Hard Wax, Lost Wax or Lost Foam.
- Sand Casting: – Sand Casting is considered the traditional method of casting. The various common methods of sand casting revolve around the types of binders used to maintain mold strength (resist the molten metal). These methods are:
- CLAY BONDED / GREEN SAND
- HARD BONDED / RESIN
- THERMO SETTING RESIN SAND / SHELL
- Die Casting: – Die Casting, also known as high pressure die casting, is a metal product formation process that involves the pressurized filling of a mold cavity with molten metal to create a formed product.
The main points we look at when deciding between Sand and Investment Casting are:
- The size of the part – Investment casting is best suited for small parts up to a maximum of 80 kgs and 1.2 metres in length. Larger parts create too much pressure and distortion of the walls of the mold. Larger castings are best made as a sand cast.
- Tolerances – Lower tolerances and a better surface finish can be achieved using the investment method.
- Cost – As a general rule we can produce investment castings at a better price than sand castings. We only source castings from those who make them better than everyone else. This means that our sand castings come from countries where the costs of production tend to be higher than countries that produce high quality investment castings, thus they are more expensive.
Advantages of Casting:-
- No real upper size limit in casting weight
- Large range of alloy choices
- As forgings remain solid, custom alloys are far more difficult to get into production whereas with casting, alloys including Chrome, Nickel and Moly can be added at the molten stage.
- Tooling is often less expensive than forge dies
- Smaller production “runs” required
- Complicated/complex parts are no problem
For general GET as well as large and complex components – casting is a fantastic method of manufacture.
Forging:-

Steel Forging Method
Forging is the application of thermal and mechanical energy to steel billets or ingots to cause the material to change shape while in a solid state using high pressure, either by striking it with a hammer or by pressing it with a die. The material is often heated beforehand in order to make forging easier, but it remains solid throughout the process. Kitchen knives and other knife blades are typical examples of products made via forging. Since steel can either be forged or cast, manufacturers usually specify the actual material grade and type as “cast steel” or “forged steel” to clarify which process was utilized.
Applications of Forging: –
Forging offers uniformity of composition and structure. Forging results in metallurgical recrystallization and grain refinement as a result of the thermal cycle and deformation process. This strengthens the resulting steel product particularly in terms of impact and shear strength. Forged steel is generally stronger and more reliable than castings and plate steel due to the fact that the grain flows of the steel are altered, conforming to the shape of the part.
Advantages of forging: –
- Generally tougher than alternatives
- Will handle impact better than castings
- The nature of forging excludes the occurrence of porosity, shrinkage, cavities and cold pour issues.
- The tight grain structure of forgings making it mechanically strong. There is less need for expensive alloys to attain high strength components.
- The tight grain structure offers great wear resistance without the need to make products “superhard” We have found that, on a blank HRC 38-42 forged grinder insert wear/wash is about the same as a high alloy HRC 46-50 cast grinder insert. The difference being a HRC 46-50 casting does not have the ductility to handle high impact grinding.
Forging Temperature on Steel
Steel Type | Maximum forging temperature (°F / °C) | Burning temperature (°F / °C) |
1.5% carbon | 1920 / 1049 | 2080 / 1140 |
1.1% carbon | 1980 / 1082 | 2140 / 1171 |
0.9% carbon | 2050 / 1121 | 2230 / 1221 |
0.5% carbon | 2280 / 1249 | 2460 / 1349 |
0.2% carbon | 2410 / 1321 | 2680 / 1471 |
3.0% nickel steel | 2280 / 1249 | 2500 / 1371 |
3.0% nickel–chromium steel | 2280 / 1249 | 2500 / 1371 |
5.0% nickel (case-hardening) steel | 2320 / 1271 | 2640 / 1449 |
Chromium–vanadium steel | 2280 / 1249 | 2460 / 1349 |
High-speed steel | 2370 / 1299 | 2520 / 1385 |
Stainless steel | 2340 / 1282 | 2520 / 1385 |
Austenitic chromium–nickel steel | 2370 / 1299 | 2590 / 1420 |
Silico-manganese spring steel | 2280 / 1249 | 2460 / 1350 |
[Source: From Web]
How to Determine Whether Forging or Casting to be Done?
Steel products may be manufactured either by casting or forging steel. Steel casting is the process by which a metal is heated until it reaches a liquid state and then poured into a mold that shapes the desired product. In Steel forging method, steel is physically forced into shape while remaining in a solid state – although it is frequently heated.
- Forged parts had a 26% higher tensile strength than the cast parts. This means you can have stronger shackles at a lower part weight. The reason behind is when you melt metal to cast it, the grain size is free to expand. When it cools back to a solid, the grain structure is courser and more random, decreasing its strength.
- Forged parts have a 37% higher fatigue strength resulting in a factor of six longer fatigue lives. This means that a forged shackle is going to last longer.
- Cast steel only has 66% of the yield strength of forged steel. Yield strength is an indicator of what load a shackle will hold before starting to deform.
- The forged parts had a 58% reduction in area when pulled to failure. The cast parts only had a 6% reduction in area. That means there would be much greater deformation before failure in a forged part.
Strengths and Weaknesses of Forging and Casting: –
Forging | Casting | |
Strength | Good Mechanical properties (yield strength, ductility, toughness) Reliability (used for critical parts) No liquid metal treatment | Large and complex parts High production rate Design flexibility |
Weakness | Defects 1. Laps 2. Die unfill 3. Die failure 4. Piping Shape limited when undercuts or cored sections are required. Overall cost usually higher than casting. Multiple steps often required. | Defects 1. Shrinkage porosity 2. Metallic projections 3. Cracks, Hot tearing, Cold shuts 4. Laps, Oxides 5. Misruns, Insufficient volume 6. Inclusions Requires close process control and inspections (porosity may occur). |
Summary
The main difference between a steel casting and a forging is that the forging is mechanically worked after solidification. This mechanical working imparts directionality, or anisotropy, to the forging. Castings and forgings are both susceptible to manufacturing problems and misapplication by the buyer.
In general, a forging is best suited to simple configurations that can be easily worked in a die or other tooling. It is also suited to applications in which the principal applied stresses are the same as the direction of mechanical working. A casting is best suited to complex shapes, custom or tailored chemistries, and to applications that are subject to multi-axial stresses.
Casting buyers need to work closely with foundries at the design stage in order to insure that the design is able to take advantage of directional solidification. The poor quality image of castings is often the result of the buyer not understanding this process. The casting buyer must also understand that there are limitations to relying solely on NDT to verify quality. Quality is best enhanced by using tools such as solidification modeling at the design stage to insure the production of a high-quality product.
Source: [From Web]
Leave A Comment