Heat treatment of pipe depends on the way it is manufactured – hot finished or cold finished. Selection of heat treatment methods will depend on types of material and on what material properties you want to restore or further enhancement on existing properties.
In the case of Hot Finished Pipe, no heat treatment is required. As during the manufacturing process, the pipe temperature remains in the range of heat treatment temperature till the final size and thickness are achieved.
Whereas in the case of Cold Finished Pipe, heat treatment is required as per applicable ASTM standard. As the pipe is either cold drawn or temperature is not maintained in the hot finish range.
Heat treatment is the process of heating and cooling metals to change their microstructure and to bring out the physical and mechanical characteristics that make metals more desirable. The temperatures metals are heated to, and the rate of cooling after heat treatment can significantly change metal’s properties. The most common reasons that metals undergo heat treatment are to improve their strength, hardness, toughness, ductility, and corrosion resistance.
Maximum Operating Temperatures

[Maximum Operating Temperatures of Stainless Steel Grades – Source: From web]
- The temperature at which the strength starts to fall sharply is defined as the maximum service temperature.
- The strength of a material tends to fall quickly when a certain temperature is reached. This temperature limits the maximum operating temperature for which the material is useful.
- For metals the maximum operating temperature is usually around two thirds of the melting temperature.
- For prolonged loading the maximum stress will be lower because creep (permanent stretching over time) will occur.
- When a metal is subjected to a stress for long time at an elevated temperatures, it undergoes plastic deformation; this time dependent accumulation of strain is known as Creep. Creep limits the life time of components.
- The creep resistant steels for various applications like tubing, boiler drum, main steam pipe, rotors and turbine blades, castings etc. can be put in three categories based on the microstructure: ferritic, bainitic and martensitic.
- Note that the range of maximum service temperature does not mean the range of temperature in which the material must be used! It may be assumed that any operating temperature below the maximum service temperature down to zero degrees Centigrade is safe in design.
- Problems can occur when materials are used well below 0oC – for example special steels must be used to contain liquefied gases, since ordinary carbon steels may become brittle at these very low temperatures.
- The maximum service temperature is important for applications where components become hot. Jet engines, brake discs and extrusion dies are all examples of products which operate at temperatures of 400oC or more – metals and ceramics are then required. Temperatures of only 100oC are enough to cause problems for lower melting point materials such as polymers – for example, plastic cups and kettles.
Properties of Steel at Room Temperature

[Properties of Steel at Room Temperature Source: From web]
Heat Treatment Process
- Hardening:- Hardening is a metallurgical metalworking process used to increase the hardness of a metal. The hardness of a metal is directly proportional to the uniaxial yield stress at the location of the imposed strain. A harder metal will have a higher resistance to plastic deformation than a less hard metal. Precipitation hardening also known as age hardening, is one of the Hardening processes. It creates uniformity in a metal’s grain structure, making the material stronger. The process involves heating a solution treatment to high temperatures after a fast cooling process. Precipitation hardening is usually executed in an inert atmosphere at temperatures ranging from 900 degrees Fahrenheit to 1,150 degrees Fahrenheit. It can take anywhere from an hour to four hours to carry out the process. The length of time typically depends on the thickness of the metal and similar factors.
- Tempering:- Tempering is a process of heat treating, which is used to increase the toughness of iron-based alloys. Tempering is usually performed after hardening, to reduce some of the excess hardness, and is done by heating the metal to some temperature below the critical point for a certain period of time, then allowing it to cool in still air.
- Annealing:- Annealing is a form of heat treatment that brings a metal closer to its equilibrium state. It softens metal, making it more workable and providing for greater ductility. In this process, the metal is heated above its upper critical temperature to change its microstructure. Afterward, the metal is slow-cooled.
- Normalizing:-Normalizing involves heating steel, and then keeping it at that temperature for a period of time, and then cooling it in air. The resulting microstructure is a mixture of ferrite and cementite which has a higher strength and hardness, but lower ductility. Normalizing is performed on structures and structural components that will be subjected to machining, because it improves the machinability of carbon steels.
- Carburization:- Carburization is a heat treatment process in which steel or iron is heated to a temperature, below the melting point, in the presence of a liquid, solid, or gaseous material which decomposes so as to release carbon when heated to the temperature used.
- Surface Hardening:- In many engineering applications, it is necessary to have the surface of the component hard enough to resist wear and erosion, while maintaining ductility and toughness, to withstand impact and shock loading. This is known as surface hardening. This can be achieved by local austentitizing and quenching, and diffusion of hardening elements like carbon or nitrogen into the surface. Processes involved for this purpose are known as flame hardening, induction hardening, nitriding and carbonitriding.
- Quenching:- Less expensive than annealing, quenching is a heat treatment method that quickly returns metal to room temperature after it is heated above its upper critical temperature. The quenching process stops the cooling process from altering the metal’s microstructure. Quenching, which can be done with water, oil, and other media, hardens steel at the same temperature that full annealing does.
- Stress Relieving:- Stress relieving is a heat treatment process that decreases stress in metals after they have been quenched, cast, normalized, and so on. Stress is relieved by heating metal to a temperature lower than that required for transformation. After this process, the metal is then slowly cooled.
- Cryogenically Treated:- When a metal part is cryogenically treated, it is slowly cooled with liquid nitrogen. The slow cooling process helps prevent thermal stress of the metal. Next, the metal part is maintained at a temperature of roughly minus 190 degrees Celsius for about a day. When it is later heat tempered, the metal part undergoes an increase of temperature up to approximately 149 degrees Celsius. This helps to lower the amount of brittleness that may be caused when martensite forms during cryogenic treatment.
- Or Combination of these.
How Does Heat Affect Metal
Metals are elements or compounds with excellent conductivity for both electricity and heat, making them useful for a wide range of practical purposes. The electrical, magnetic and structural properties of metals can change with temperature and thereby provide useful properties for technological devices. Understanding the impacts of temperature on the properties of metals gives you a deeper appreciation for why they’re so widely-used in the modern world.
- Thermal Expansion – Heating metal can increase its volume, length and surface area, as the heat displaces atoms from their usual position which alters the structure.
- Magnetism – Iron, cobalt and nickel are all naturally magnetic materials, or ferromagnetic materials. When heat is applied to them it can reduce their natural magnetic properties to a point so low that it is completely gone.
- Resistance – Some metals are able to effectively reduce, or halt, the flow of an electric current. This is known as resistance and how resistant a metal is depends on how quickly electrons are able to pass through it.
The following are our most widely used alloys in manufacturing industrial gaskets, their major characteristics, temperature limits and approximate Brinell hardness (HB).
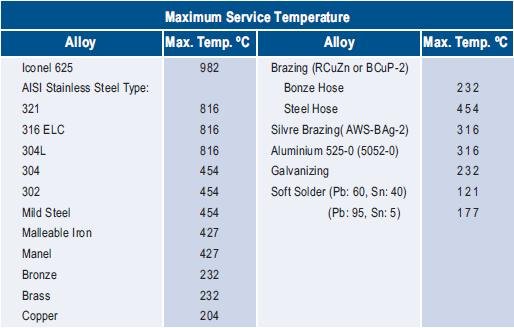
Maximum Operating Temperatures of Steel [Source: From web]
Material | Temperature Limit | Approximate Hardness | Features |
Carbon Steel | 900° F (500° C) | 90 to 120 HB | Material frequently used in manufacturing jacketed gaskets and Ring Joints. Due to its low resistance to corrosion it should not be used in water, diluted acids or saline solutions. It may be used in some alkalis and in some concentrated acids. |
Stainless Steel AISI 304 | 790° F (420° C) | 160 HB | Alloy with 18% Cr and 8% Ni is the material most used in the manufacturing of industrial gaskets due to its excellent resistance to corrosion, low cost and availability in the market. Its maximum operating temperature is 1400° F (760° C) |
Stainless Steel AISI 304L | 1400° F (760° C) | 160 HB and in some cases,140 HB | It has the same resistance to corrosion as the AISI 304. Since its Carbon content is limited to 0.03%, it has less Intergranular Carbon precipitation and therefore less Intergranular Corrosion. It is susceptible to Stress Corrosion. |
Stainless Steel AISI 316 | 1400° F (760° C) | 160 HB | This alloy with 18% Ni, 13% Cr and 2% Mo, offers excellent resistance to corrosion. It can have carbonate precipitation at temperatures between 860° F (460° C) and 1650° F (900° C), under severe corrosion conditions. |
Stainless Steel AISI 316L | 1400° F (760° C) | 160 HB | It has the same chemical composition as the AISI 316 but its Carbon content is limited to 0.03%, which inhibits the Intergranular Carbon precipitation and consequently, the Intergranular Corrosion. |
Stainless Steel AISI 321 | 1500°F (815°C) | 160 HB | Austenitic stainless steel alloy with 18% Cr and 10% Ni stabilized with Ti, which reduces the Intergranular Carbon precipitation and also the Intergranular Corrosion. |
Stainless Steel AISI 347 | 1550° F (815° C) | 160 HB | Alloy similar to the AISI 304 stabilized with Cb and Ta to reduce carbonate precipitation and Intergranular Corrosion. It is subject to Stress Corrosion. Has good performance in high temperature corrosive service. |
Monel | 1550° F (815° C) | 95 HB | Alloy with 67% Ni and 30% Cu, it offers excellent resistance to the majority of acids and alkalis, except to extremely oxidant acids. Subject to stress corrosion and therefore should not be used in the presence of fluorine-silicon acid and Mercury. In combination with PTFE, it is used frequently in spiral wound gaskets for severe corrosion services, such as Hydrofluoric acid. |
Nickel 200 | 1400 F (760° C) | 110 HB | Alloy with 99% Ni, offers great resistance to caustic solutions, even thought it does not have the same global resistance of Monel. It is also used in spiral wound and jacketed gaskets for special applications. |
Copper | 500° F (260° C) | 80 HB | Material often used in small dimension gaskets, where the maximum seating stress is limited. |
Aluminium | 860° F (460° C) | 35 HB | Due to its excellent resistance to corrosion and easy handling it is very often used in manufacturing gaskets. |
Inconel | 2000° F (1100° C) | 150 HB | Alloy with 77% Ni, 15% Cr and 7% Fe, it has excellent corrosion resistance from cryogenic to high temperatures. |
Titanium | 2000° F (1100° C) | 215 HB | Metal with excellent corrosion properties in elevated temperatures, oxidant service, Nitric acid and caustic solutions. |
Metallica also provides the following services:
- CNC Machining and EDM Machining Service
- Surface Treatment: Metal Polishing (Metal Mirror Polished, Brushed Metal Finishing), Shot Blasting, Sandblasting, Spray Painting, Powder Coating, Thermal Spraying, Anodizing, Chrome Plating, Nickel Electroplating / Electroless Nickel Plating, Hot-Dip Galvanizing, Copper Plating, Phosphorizing, Electrophoresis and Passivation
- Assembly
- Packing
- Testing Report, QC Report
- Heat treatment solution, includes annealing, tempering, normalizing, quenching, case hardening, stress relieving, precipitation strengthening and so on
- Supports various materials for metal heat treating service, includes: iron, carbon steel, stainless steel, alloy steel, aluminum (alloy), copper (alloy), magnesium (alloy), titanium (alloy) and other alloys.